Sports cars are characterized by unique design and performance. However, powerful engines come with increased noise levels. Owners of such vehicles often struggle with excessive sound coming from the engine compartment, exhaust system, and road noise. Effective soundproofing becomes essential for driving comfort.
Butyl mats and rubber foams offer a modern solution to the noise problem. These materials are highly effective at dampening sound. Professional application of these products significantly reduces cabin noise levels while preserving the vehicle’s sporty character.
The soundproofing process requires proper preparation and precise installation. Every step is crucial to the final result. Correct use of butyl mats and rubber foams leads to a noticeable improvement in comfort. Investing in professional soundproofing also increases the vehicle’s resale value.
Why Sports Cars Require a Special Approach to Soundproofing
The construction of sports cars differs significantly from regular passenger vehicles. Manufacturers focus primarily on performance and driving dynamics. Acoustic comfort often takes a back seat. The result is an increased noise level inside the passenger cabin.
Diesel engines in sports cars generate more noise than standard power units. Higher power translates into stronger vibrations and noise. Exhaust systems are designed for efficiency, not quietness. Sport suspensions transmit more road vibrations directly into the cabin.
Specific Noise Sources in Sports Vehicles
The engine compartment is the main source of excessive noise in sports cars. High-revving power units produce intense mechanical sounds. Turbocharging further raises acoustic levels. Intercooler cooling and ventilation systems generate additional noise.
The exhaust system in sports cars often features smaller mufflers. Sport headers and exhaust pipes transmit more sound into the cabin. Acoustic resonators are sometimes limited or completely removed. The result is a distinctive but often excessively loud engine sound.
The chassis and sport suspension transmit significantly more vibrations from the road surface. Stiffer springs and shock absorbers do not filter vibrations as effectively. Wider low-profile tires increase rolling noise. Aerodynamic add-ons can generate additional air turbulence sounds.
The Impact of Noise on Driving Comfort and Safety
Excessive cabin noise negatively affects driver concentration. Prolonged exposure to loud sounds causes hearing fatigue. Conversations with passengers become difficult or impossible. The audio system must operate at higher volume levels.
Noise masks important sounds from the vehicle’s surroundings. Audible signals from other road users may go unheard. Unusual noises from the engine or drivetrain remain unnoticed. Driving safety is significantly compromised.
Prolonged driving in a noisy vehicle leads to stress and tension. The body responds to continuous noise with increased cortisol levels. The quality of the trip drops drastically, especially on longer routes. The vehicle’s resale value also decreases.
Properties of Butyl Mats and Their Use in Automotive Applications
Butyl mats represent the latest technology in vehicle soundproofing. This material is characterized by exceptional flexibility and adhesion. Butyl exhibits excellent vibration damping properties. Its molecular structure ensures long-lasting effectiveness.
The operating temperature range of butyl mats spans from -40°C to +150°C. The material maintains flexibility under extreme weather conditions. Resistance to moisture and corrosion makes it ideal for automotive applications. Chemical stability guarantees many years of durability without degradation of properties.
Mechanism of Action of Butyl Mats
Butyl mats work by converting vibration energy into heat. The flexible structure of the material absorbs mechanical vibrations originating from the engine. Butyl molecules move relative to each other, dissipating kinetic energy. This process effectively eliminates resonances in the body panels.
The thickness of the butyl mat directly affects damping effectiveness. Thinner layers work efficiently at higher sound frequencies. Thicker mats handle low tones and structural vibrations better. Optimal thickness is selected depending on the application area.
The adhesive layer of butyl mats provides a durable bond with metal surfaces. Special components increase adhesion to various construction materials. The absence of air bubbles under the mat ensures maximum effectiveness. Professional installation eliminates the risk of material detachment.
Applications of Butyl Mats in Different Vehicle Areas
Car doors are the primary application area for butyl mats. Large sheet metal surfaces create acoustic resonators that require damping. Mats are applied to the inner door panels at key points. Damping effectiveness reaches 15-20 decibels depending on material quality.
Key installation locations for butyl mats:
- Front and rear door panels
- Passenger cabin floor
- Engine compartment bulkhead walls
- Driveshaft tunnel and fuel tank
- Trunk lid and engine hood
The engine compartment requires special mats resistant to high temperatures. Application on the bulkhead significantly reduces noise penetration into the cabin. Mats are also installed on the inner side of the engine hood. The acoustic effect is immediately noticeable after starting the engine.
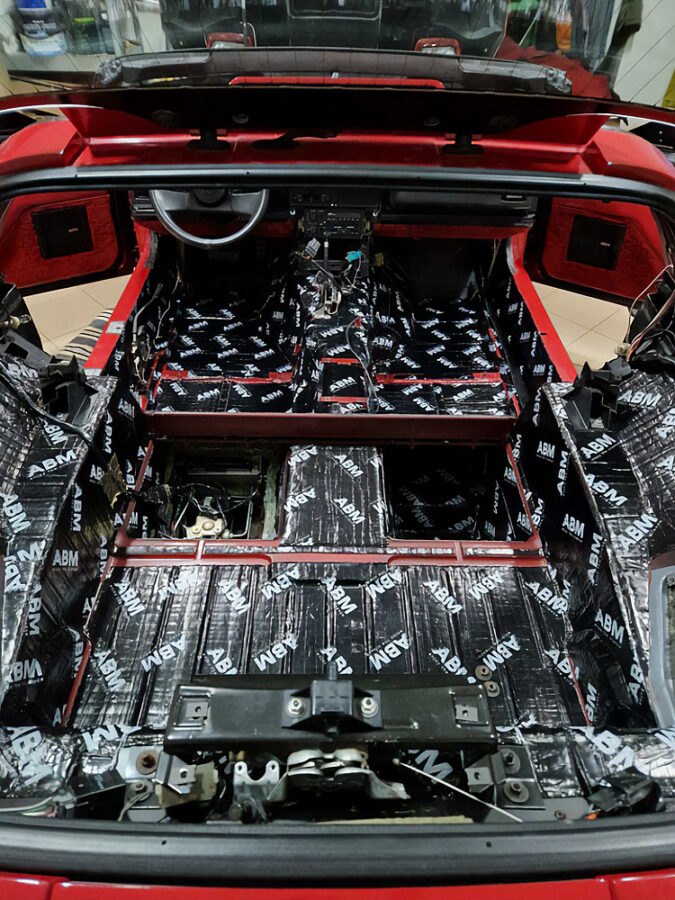
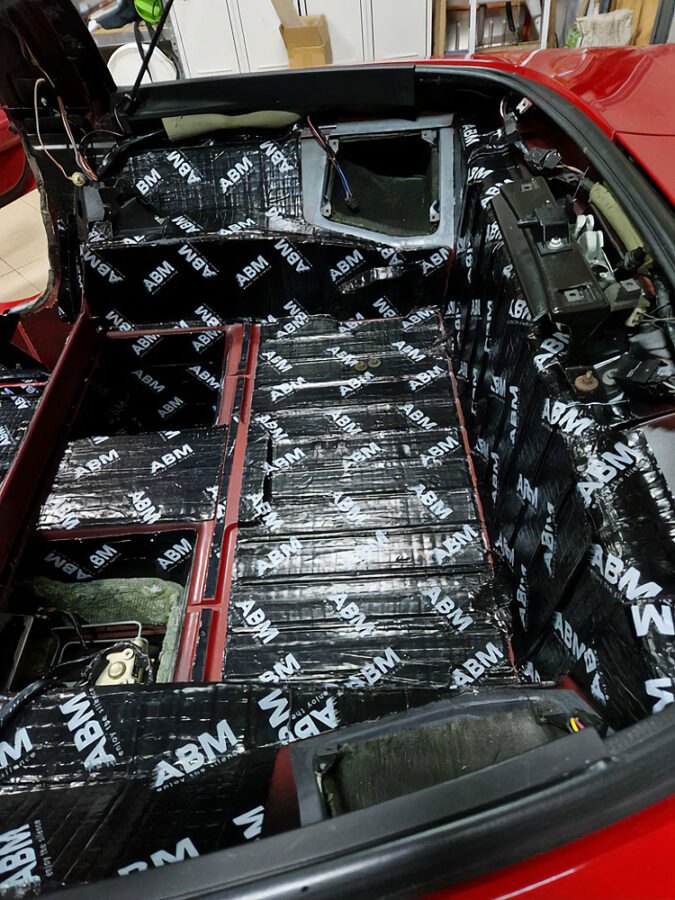
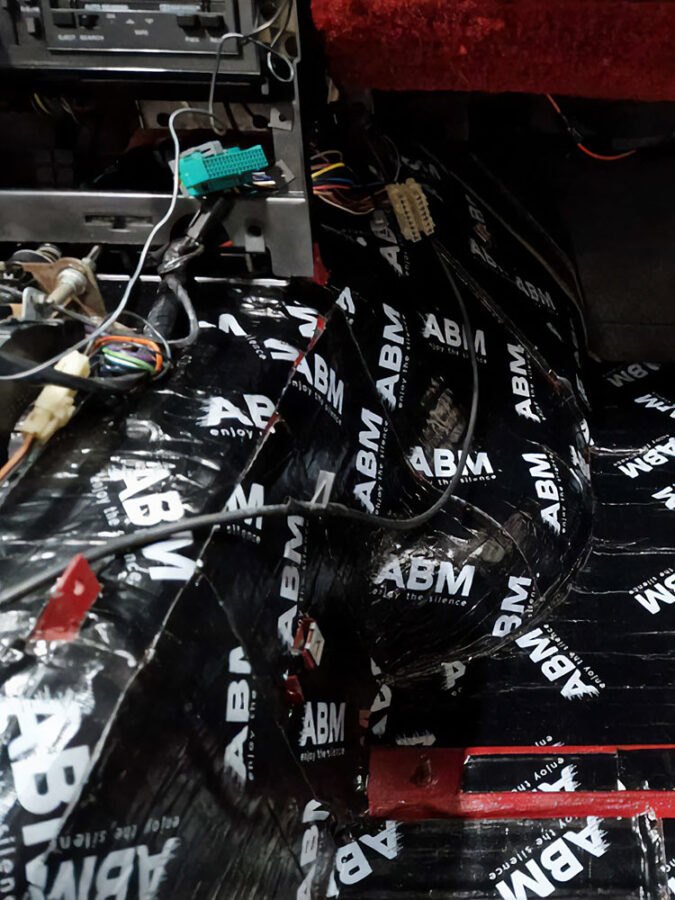
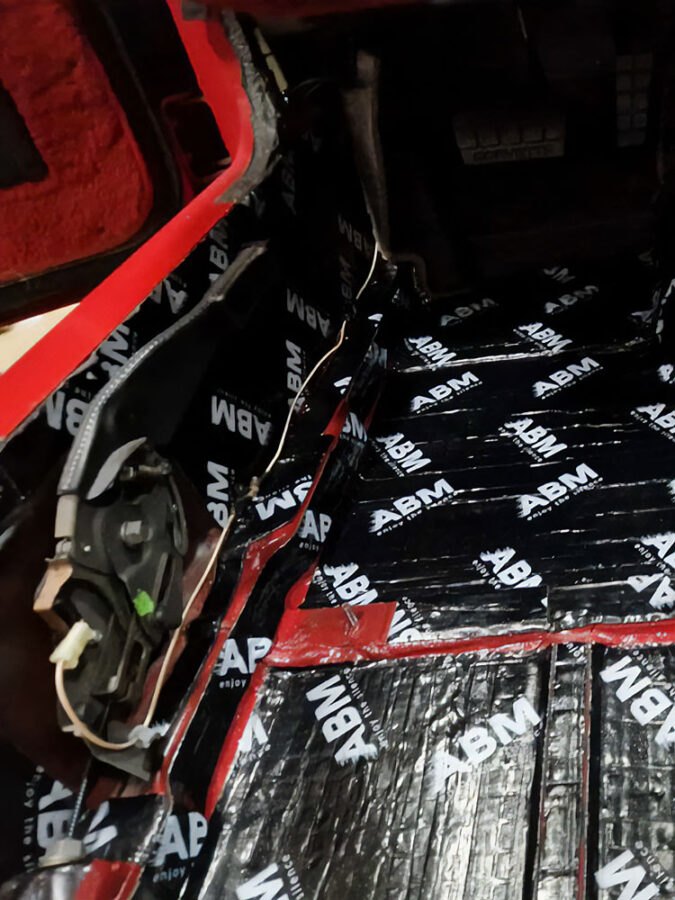
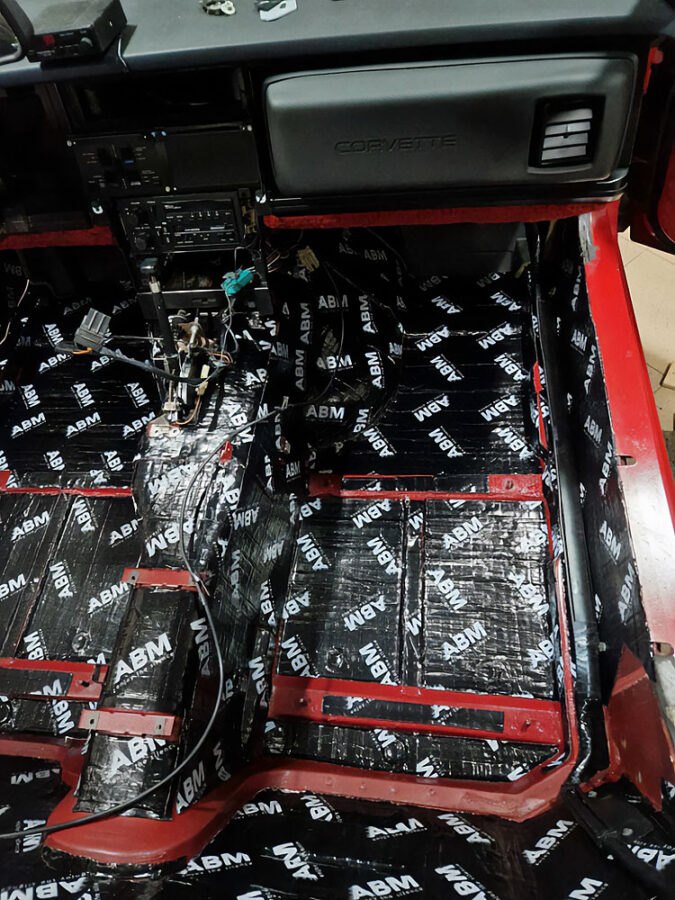
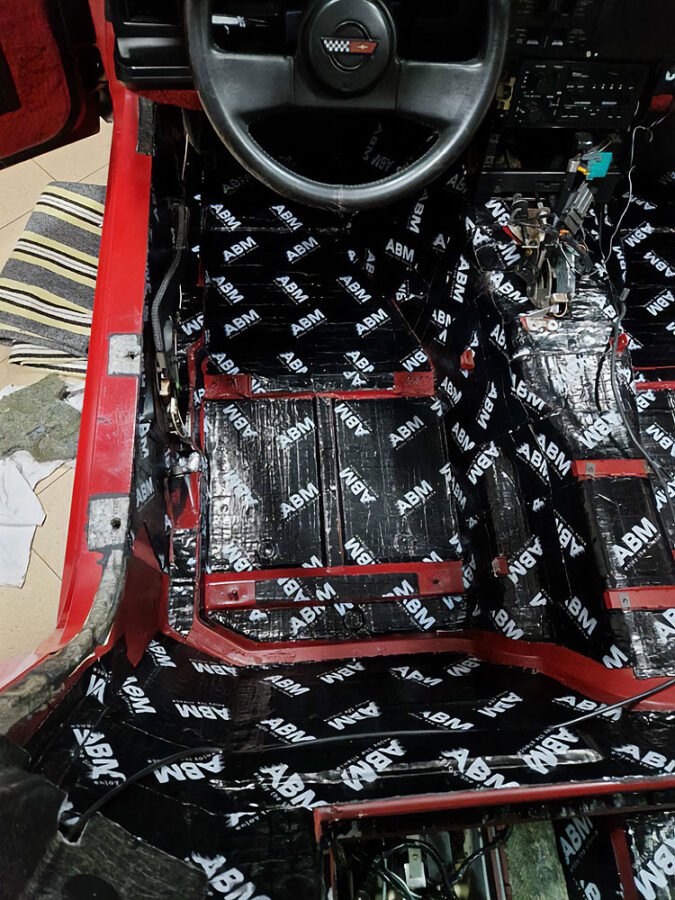
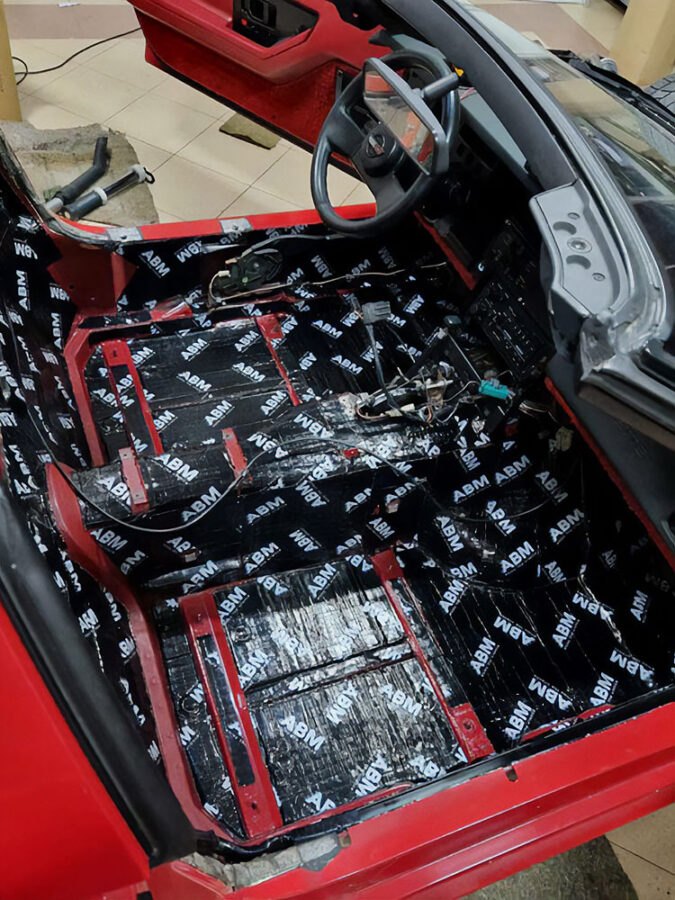
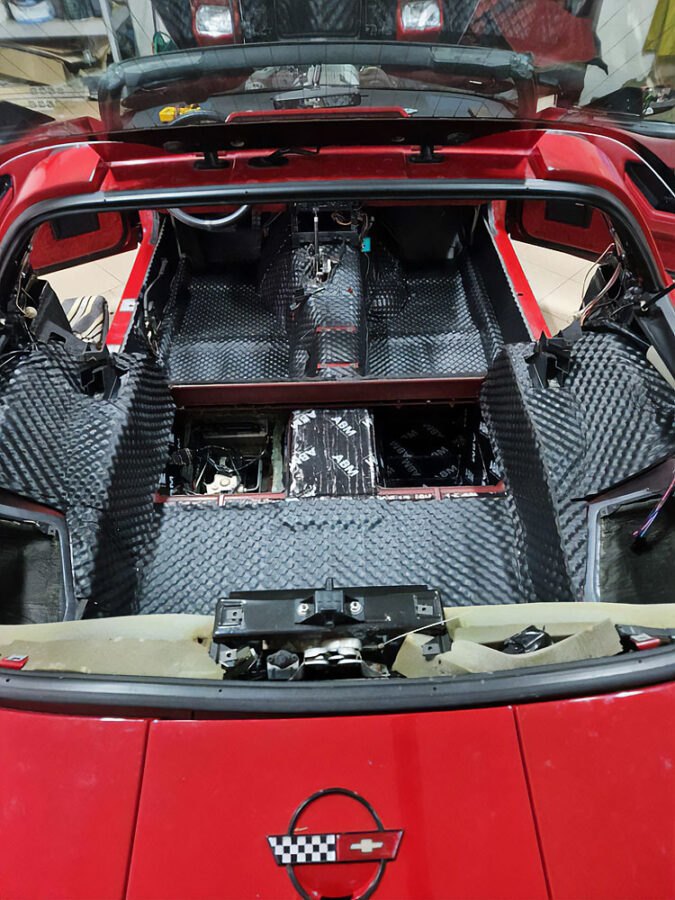
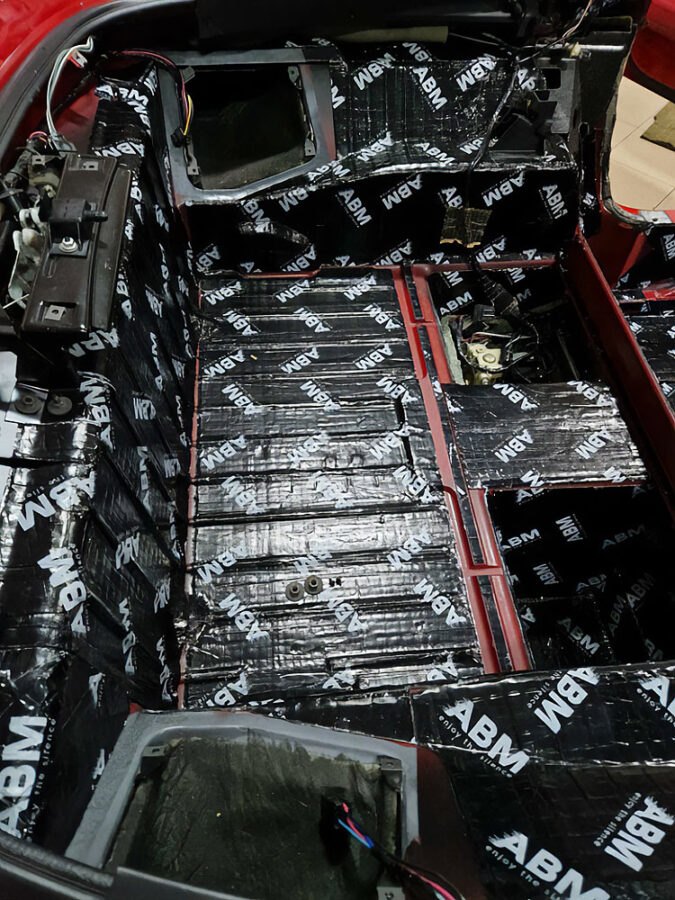
The vehicle floor transmits vibrations from the drivetrain and engine. Butyl mats applied under carpet liners eliminate resonances. Areas above the driveshaft tunnel and fuel tank are particularly important. Professional installation requires removal of seats and carpets.
Comparison of Butyl Mats with Other Soundproofing Materials
Traditional bituminous materials are characterized by a limited operating temperature range. At high temperatures, they may soften and flow. Butyl mats maintain stability throughout the entire operating temperature range. The absence of unpleasant odors is an additional advantage.
Polyurethane foams primarily act as sound absorbers, not vibration dampers. Combining butyl mats with rubber foams produces a synergistic effect. Butyl eliminates vibrations, while the foam absorbs sound waves. This comprehensive solution ensures maximum soundproofing effectiveness.
Mineral wool and fiberglass require additional moisture protection. Butyl mats are completely waterproof and do not require coverings. Installation is much simpler and faster than with traditional materials. There is no risk of skin irritation when working with butyl.
Types of Rubber Foams Best for Soundproofing in Vehicles
Rubber foams form the second layer of vehicle soundproofing systems. These materials feature a closed-cell cellular structure. Air trapped within the cells effectively absorbs sound waves. The material’s flexibility ensures excellent conformity to irregular surfaces.
The density of rubber foam determines its acoustic and mechanical properties. Lower density provides better absorption of high frequencies. Higher density more effectively handles low tones and vibrations. Optimal density is selected based on the specific application.
Structure and Properties of Rubber Foams
The closed cells in rubber foams create a natural barrier to sound waves. Acoustic energy is converted into heat through internal friction. The flexible structure allows repeated deformation without loss of properties. Aging resistance ensures long-lasting effectiveness.
The sound absorption coefficient of rubber foams reaches 0.9 for frequencies between 1000-4000 Hz. The material effectively dampens high-frequency engine noise. Low frequencies require thicker foam for optimal results. Combining different thicknesses allows for broadband attenuation.
Resistance to temperatures from -50°C to +120°C makes these foams suitable for automotive use. The material does not lose flexibility in cold winter temperatures. High temperatures do not degrade the cellular structure. Dimensional stability remains preserved across the entire temperature range.
Classification of Foams by Application
Self-adhesive foams have an adhesive layer protected by a release film. Installation is quick and does not require additional adhesives. The adhesive layer provides a durable bond with various surfaces. The thickness of the adhesive layer affects the final damping effectiveness.
Types of Rubber Foams by Thickness:
- Thin (5-10 mm) – for small spaces and details
- Medium (15-25 mm) – universal use in the cabin
- Thick (30-50 mm) – for intensive damping in the engine compartment
Foams with varying hardness are used for specialized applications. Soft foams better conform to irregular surfaces. Hard foams maintain shape under mechanical load. Hardness selection depends on location and installation requirements.
Foams with an aluminum layer reflect heat radiating from the exhaust system. The metallic surface also increases the reflection of sound waves. Their use near hot engine components is particularly justified. Additional thermal protection extends the material’s lifespan.
Tip: Before selecting the thickness of rubber foam, measure the available installation space. Foam that is too thick may hinder the installation of finishing panels or cause their deformation.
Butyl Mats and ABM Insulation Rubber Foams in the ABM Insulation Store
ABM Insulation offers a comprehensive range of vehicle soundproofing materials. The products are characterized by high quality and effectiveness. ABM Professional butyl mats have been specially developed for automotive applications. The insulating rubber foams provide excellent sound absorption.
All materials available in the offer have undergone rigorous quality tests. Certificates and approvals confirm compliance with European standards. Stable technical parameters guarantee predictable acoustic performance. Professional advice helps in selecting optimal solutions.
ABM Professional Butyl Mats
ABM Professional mats represent the highest quality butyl mats available on the market. A thickness of 2.3 mm provides an optimal balance between effectiveness and weight. The adhesive layer features exceptional adhesion to metal surfaces. Operating temperatures from -40°C to +150°C cover all operating conditions.
The multilayer structure of the ABM Professional mat consists of a butyl core and a reinforcing layer. The aluminum foil increases stiffness and facilitates shaping on curved surfaces. Special cuts allow precise fitting to complex shapes. The lack of odor makes the material user-friendly during installation.
The vibration damping effectiveness reaches 25 dB in the frequency range of 100-1000 Hz. The mechanical loss factor is 0.8, placing the material among the top available solutions. Long-term parameter stability guarantees years of effectiveness. Moisture resistance eliminates the risk of corrosion under the mat.
Butyl Soundproofing Mats ABM Professional in the ABM Insulation store
ABM Xtreme Butyl Mats
ABM Xtreme mats are designed for the most demanding applications. Increased thickness of 4 mm ensures maximum damping effectiveness. The reinforced adhesive layer withstands extreme temperatures and vibrations. Use in racing and sports cars delivers spectacular results.
The special butyl formula in the Xtreme series features enhanced flexibility. The material perfectly conforms to surfaces with complex shapes. The thicker aluminum layer provides additional thermal protection. The mirror-like effect reflects heat radiating from the exhaust system.
The extended operating temperature up to +180°C allows installation in close proximity to the engine. Resistance to oils and fuels eliminates the risk of degradation from accidental leaks. The vibration damping coefficient exceeds 30 dB for resonant frequencies. Investing in the Xtreme series pays off through a significant improvement in comfort.
Butyl Soundproofing Mats ABM Xtreme in the ABM Insulation store
Insulating Rubber Foams
ABM’s range of insulating rubber foams includes various thicknesses and densities. The closed-cell structure provides excellent sound absorption. The self-adhesive layer facilitates installation without additional tools. The material’s flexibility allows application on irregular surfaces.
Foams with a thickness of 10 mm are ideal for soundproofing doors and side panels. The 20 mm variant effectively reduces noise in floors and cabin walls. The 30 mm thickness ensures maximum absorption in the engine compartment. All variants feature identical quality and durability.
The noise reduction coefficient (NRC) is 0.85 for ABM foams. The material effectively eliminates echoes and reverberation inside the vehicle cabin. Moisture and UV resistance ensure long-lasting parameter stability. Neutral odor and absence of harmful emissions guarantee safe use.
Insulation Rubber Foams in the ABM Insulation store
Installation Accessories
ABM’s comprehensive accessory offer facilitates professional installation of soundproofing materials. Pressure rollers ensure even distribution of pressure during application. Cutting knives with replaceable blades allow precise mat cutting. Cleaning agents prepare surfaces for installation.
Butyl tapes are used to seal gaps and joints between panels. Contact adhesives enable foam installation on vertical surfaces. Protective films shield materials from mechanical damage. Professional tools guarantee workmanship quality at the level of specialized workshops.
Tip: Before starting work, it is advisable to order a complete set of tools and accessories. Professional equipment significantly eases installation and impacts the final soundproofing quality.
Accessories in the ABM Insulation store
Surface Preparation Before Installing Soundproofing Materials
Proper surface preparation is the foundation of effective vehicle soundproofing. The adhesion quality of materials depends directly on the cleanliness and condition of the substrate. Neglecting this preparatory stage leads to premature mat detachment. Investing in thorough cleaning pays off many times over through durable installation.
Metal surfaces in vehicles are often covered with protective layers and contaminants. Factory anti-corrosion coatings can limit adhesive bonding. Dust, grease, and production residues must be removed before assembly. Surface temperature also affects the quality of the adhesive bond.
Disassembly of Finishing Components
Access to surfaces intended for soundproofing requires disassembling finishing panels. Car doors require removal of upholstery and vapor barrier films. The cabin floor must be cleared of carpet coverings and insulation. Systematic labeling of components facilitates later assembly.
Electronic systems in doors require careful disconnection before disassembly. Speaker wires and central locking cables may be damaged. Photographing connections before disassembly helps ensure proper reassembly. Protecting wires from contamination is crucial.
Specialized tools significantly facilitate damage-free disassembly. Plastic pry tools protect surfaces from scratches. Torx and Allen wrenches are essential for modern vehicles. Work organization and workstation preparation affect process efficiency.
Cleaning and Degreasing Surfaces
Mechanical surface cleaning removes loose contaminants and surface rust. Wire brushes of varying stiffness are matched to the surface type. Sandpaper with a grit of 240-400 provides appropriate roughness for adhesives. Dust generated during sanding must be thoroughly removed.
Solvent degreasing removes invisible layers of oils and greases. Isopropanol or acetone effectively dissolve most organic contaminants. Applying solvent with a lint-free cloth prevents fiber residue. Repeated wiping ensures complete cleaning.
Surface cleaning sequence:
- Removal of loose contaminants with a brush
- Sanding with sandpaper
- Vacuuming and dust removal
- Degreasing with solvent
- Drying and cleanliness inspection
Quality control of cleaning involves checking the adhesion of test tape. Strongly adhered tape should not peel off when pulled. The water drop test checks the effectiveness of surface degreasing. Even spreading of water droplets indicates proper preparation.
Environmental Conditions During Assembly
Ambient temperature significantly affects adhesive properties in butyl mats. The optimal installation temperature is 18-25°C for most materials. Low temperatures slow bonding processes and may reduce adhesion strength. High temperatures accelerate curing but complicate positioning.
Relative air humidity should not exceed 60% during installation. Excess moisture can condense on metal surfaces. Water droplets under the mat prevent proper bonding. Heating or dehumidifying the workspace may be necessary.
Workstation ventilation ensures removal of solvent vapors. Vapor concentration can impact work quality and safety. Carbon filters in ventilation systems absorb harmful substances. Working in enclosed spaces requires special caution.
Tip: Metal surfaces can be gently warmed with a hairdryer before installing the mats. A warm surface ensures better adhesive bonding and facilitates shaping the material on curved parts.
Step-by-step installation of butyl mats in key areas of the car
Installing butyl mats requires a systematic approach and precise execution of each step. The order of material application is crucial for the final result. Starting with the largest surfaces allows gaining experience. Gradually moving to more complex areas ensures high-quality installation.
Each area in the vehicle has specific installation requirements. Doors require precise fitting around openings and edges. The floor must be protected against moisture and mechanical damage. The engine compartment requires materials resistant to high temperatures.
Installation in vehicle doors
Car doors are a primary location for applying butyl mats. Large metal surfaces create resonators that need damping. Installation begins with the largest inner panels. The mat is applied from the center toward the edges with even pressure.
Technological holes in the doors require precise cutting in the mat. A paper template helps transfer the shape onto the material. A knife with a replaceable blade ensures clean cuts without fraying. Leaving a 2-3 mm material allowance allows for accurate fitting.
The edges of butyl mats must be firmly pressed against the surface. A pressure roller eliminates air bubbles under the material. Special attention should be paid to corners and bends. Material temperature affects ease of shaping on curved surfaces.
Application on cabin floor
The vehicle floor transmits vibrations from the engine, drivetrain, and road surface. Butyl mats are applied directly onto floor panels. The driveshaft tunnel requires special attention due to intense vibrations. Areas above the fuel tank also need soundproofing.
Removing seats and center console provides full access to the floor. Electrical wiring must be protected from damage. The mat is cut into smaller segments to facilitate installation. Overlapping segments by 10-15 mm eliminates acoustic bridges.
Installation location | Mat thickness | Surface coverage | Damping effect |
---|---|---|---|
Driveshaft tunnel | 4 mm | 100% | 20-25 dB |
Front floor | 2-3 mm | 80% | 15-20 dB |
Rear floor | 2-3 mm | 60% | 10-15 dB |
Areas exposed to moisture require additional edge sealing. Butyl tape protects against water penetration under the mat. Leak testing after installation eliminates corrosion risk. Proper ventilation prevents condensation buildup.
Engine compartment soundproofing
The engine compartment generates the most intense vibrations and noise in the vehicle. The partition wall between the engine and the cabin requires thick mats with a high operating temperature. The inside of the engine hood should also be soundproofed. Materials must withstand temperatures up to 150°C.
Access to the partition wall requires partial disassembly of engine components. Wires and tubes must be carefully disconnected and secured. The mat is cut into segments tailored to the shape of the wall. Pass-through holes require precise cutting in the material.
The engine hood is mounted from the inside after thorough cleaning. The high surface temperature requires cooling before installation. A mat with an aluminum layer reflects heat and increases durability. Pressure must be even across the entire surface.
Tip: Before installing mats in the engine compartment, it is advisable to check surface temperatures after driving. A non-contact thermometer allows identification of the hottest spots requiring special materials.
Rubber Foam Application Techniques for Maximum Effectiveness
Rubber foams form the second layer of the soundproofing system, applied after installing butyl mats. These materials require different installation techniques due to their cellular structure. Proper foam application ensures maximum sound absorption. Combining them with butyl mats produces a synergistic damping effect.
The thickness and density of the foam are selected depending on the application area. Thin foams work effectively in confined spaces. Thick layers provide intense absorption in large cavities. The self-adhesive layer facilitates installation but requires proper surface preparation.
Preparing Foams for Installation
Rubber foams are supplied in sheets of standard dimensions. Cutting into smaller segments facilitates application in complex areas. A knife with a long blade ensures straight cuts without tearing the structure. A cardboard template allows precise shape fitting.
Foam temperature affects flexibility and ease of installation. Material stored at low temperatures requires acclimatization. The optimal working temperature is 18-25°C for most foams. Heating with a hairdryer increases flexibility during shaping.
The adhesive layer is protected by a silicone film removed immediately before installation. Premature removal leads to adhesive contamination. Gradual exposure of the adhesive surface facilitates positioning. The glue activates immediately upon contact with the surface.
Application Techniques in Various Areas
Vehicle doors require foams tailored to irregular panel shapes. Radial cutting allows forming on curved surfaces. Foams are applied between the frame and finishing panel. Thickness is selected so as not to hinder upholstery installation.
The spaces behind door upholstery often have limited height. Thin foams 10-15 mm thick effectively absorb high-frequency sounds. Applying multiple layers increases effectiveness without excessively increasing thickness. Each layer must be pressed firmly against the substrate.
Rubber Foam Cutting Techniques:
- Straight cutting – for flat surfaces
- Radial cutting – for curved surfaces
- Wedge cutting – for corners and bends
- Mosaic cutting – for surfaces with complex shapes
The cabin floor requires thicker foams due to intense vibrations. The 20-30 mm options provide effective low-frequency absorption. Foams are placed between butyl mats and carpets. Tight connections eliminate acoustic bridges.
Quality Control and Finishing
Adhesion testing of the foams involves gently trying to peel off the edges. Properly applied foam should not detach from the substrate. Areas with poor adhesion require additional pressure or replacement. Inspection is performed 24 hours after installation.
Finishing the foam edges affects the aesthetics and durability of the installation. Sharp edges may tear during use. Rounding with a knife or sandpaper increases durability. Finishing tapes protect edges from damage.
The total thickness of insulation layers must not exceed installation capabilities. Excessively thick layers make it difficult or impossible to install finishing panels. Measuring thickness at key points prevents problems. Any adjustments are made before upholstery installation.
Tip: Rubber foams can be slightly compressed during finishing panel installation. The material’s elasticity ensures a tight fill of spaces and eliminates panel vibrations that could generate additional noise.
The Impact of Professional Soundproofing on Driving Comfort and Vehicle Value
Professional soundproofing of a sports car brings tangible benefits in daily use. Noise reduction inside the cabin reaches 15-25 decibels depending on the scope of work. Acoustic comfort improvement is immediately noticeable to all passengers. Long trips become significantly less tiring for both driver and passengers.
The sound quality of the audio system drastically improves after vehicle soundproofing. Eliminating background noise allows listening to music at lower volume levels. Phone conversations via hands-free systems become clearer. Passengers can hold normal conversations without raising their voices.
Improvement of Acoustic Comfort
Reducing engine noise inside the cabin allows better concentration while driving. The driver experiences less fatigue on long trips due to lower acoustic stress levels. Passengers can rest or work in comfortable conditions. The travel experience rises to the level of luxury vehicles.
Eliminating vibrations transmitted through the body enhances physical comfort. Vibrations of seats and finishing panels are significantly reduced. Items in compartments stop rattling and shifting. The overall impression of vehicle solidity noticeably improves.
The ability to hear important environmental sounds remains preserved. Audible signals from other vehicles are clearly heard. Unusual noises from the engine or drivetrain are not masked. Driving safety improves thanks to better acoustic perception.
Impact on Vehicle Market Value
Professional soundproofing increases the resale value of the vehicle. Potential buyers appreciate acoustic comfort as a significant advantage. Sports cars with soundproofing achieve higher sale prices. Investing in high-quality materials pays off upon resale.
Documentation of completed work enhances the credibility of modifications. Invoices for materials and services confirm the quality of the solutions used. Photos from the installation process document professional execution. Warranties on materials and labor provide additional value.
Vehicle Type | Value Increase | Payback Period | Additional Benefits |
---|---|---|---|
Sports Car | 8-12% | 3-5 years | Comfort, prestige |
Luxury Vehicle | 5-8% | 4-6 years | Audio quality |
Utility Vehicle | 10-15% | 2-4 years | Reduced fatigue |
Material quality certificates confirm compliance with European standards. Safety certifications eliminate concerns about harmful substance emissions. Professional workmanship does not negatively affect the vehicle’s warranty. All modifications are reversible without damage.
Long-Term Operational Benefits
Soundproofing protects interior components from premature wear. Vibrations are a primary cause of loosening joints and damage. Trim panels maintain stability for a longer time. Repair and maintenance costs are reduced.
Acoustic insulation positively affects the vehicle’s thermal insulation. Butyl mats and rubber foams limit heat transfer. The cabin heats up faster in winter and stays cooler on hot days. Air conditioning efficiency improves, resulting in fuel savings.
Corrosion protection is an additional benefit of professional soundproofing. Butyl mats protect metal surfaces from moisture and road salt. Rubber foams do not absorb water and do not promote rust development. The durability of the bodywork is extended, especially in harsh climatic conditions.
Tip: Documenting the soundproofing process with photos before, during, and after installation creates valuable material when selling the vehicle. Potential buyers can assess the quality of workmanship and the scope of materials used.
Summary
Effective soundproofing of a sports car using butyl mats and rubber foams provides a comprehensive solution to excessive noise issues. Professionally performed work delivers tangible benefits in increased driving comfort and higher vehicle value. The combination of high-quality materials with precise installation guarantees long-lasting effectiveness of the soundproofing system.
An investment in professional soundproofing pays off through improved daily vehicle use quality. Noise reduction of 15-25 decibels translates into significantly less fatigue for drivers and passengers. The ability to hold normal conversations and listen to music at lower volume levels enhances driving enjoyment. Additionally, vibration protection extends the lifespan of trim components and increases overall vehicle durability.
The selection of appropriate materials and professional installation are crucial for the final result. ABM Professional and Xtreme butyl mats combined with insulating rubber foams provide optimal damping across the entire frequency spectrum. A systematic approach to the soundproofing process, from surface preparation to quality control, ensures the durability and effectiveness of the solutions applied for years of vehicle use.